Conventional CNC Comparison
How PlasmaCAM Compares to Conventional CNC
Conventional CNC technology dates back to 1801, when the first Jacquard Loom was programmed with a chain of punch cards. Punch tape was still used to program NC machines long after digital computers were invented (as explained from firsthand experience by our tech support manager). Since its development in the 1950s, G-code and digital files gradually replaced punch cards and tape for programming CNC machines.
Today, conventional CNC machines must still be programmed. They require operators to obtain and learn several different software programs to design for and program the machines through many challenging steps. This perpetuates the same old paradigm that is especially cumbersome for plasma cutting at small shops that want to cut metal art and custom projects, not just simple, mass-produced geometric shapes.
PlasmaCAM revolutionizes the whole process with all new technology designed for the modern computer. Our DesignEdge software fully integrates the entire process from creating designs to cutting finished parts directly from drawings on screen.
The following diagrams illustrate these software differences and show why the PlasmaCAM machine is so much faster and easier to use than a conventional CNC machine. Each white box represents a software program that is required for a specific step or capability, and each arrow represents a file that must be transferred from one of these programs to another. (The DesignEdge software includes full capabilities without requiring extra programs and steps.)
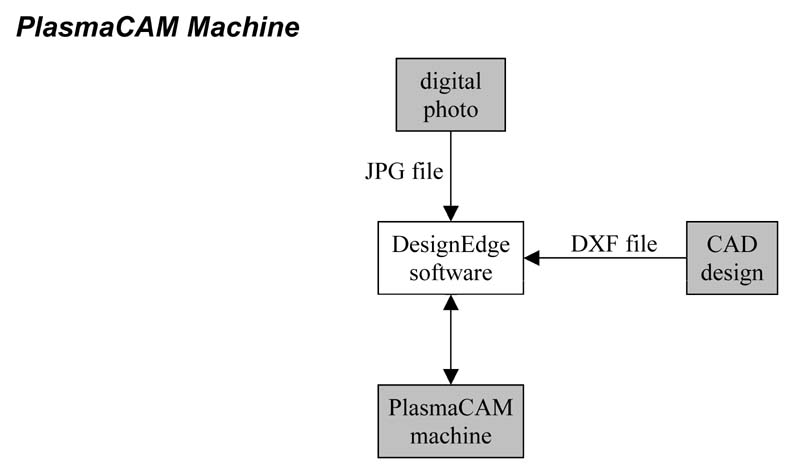
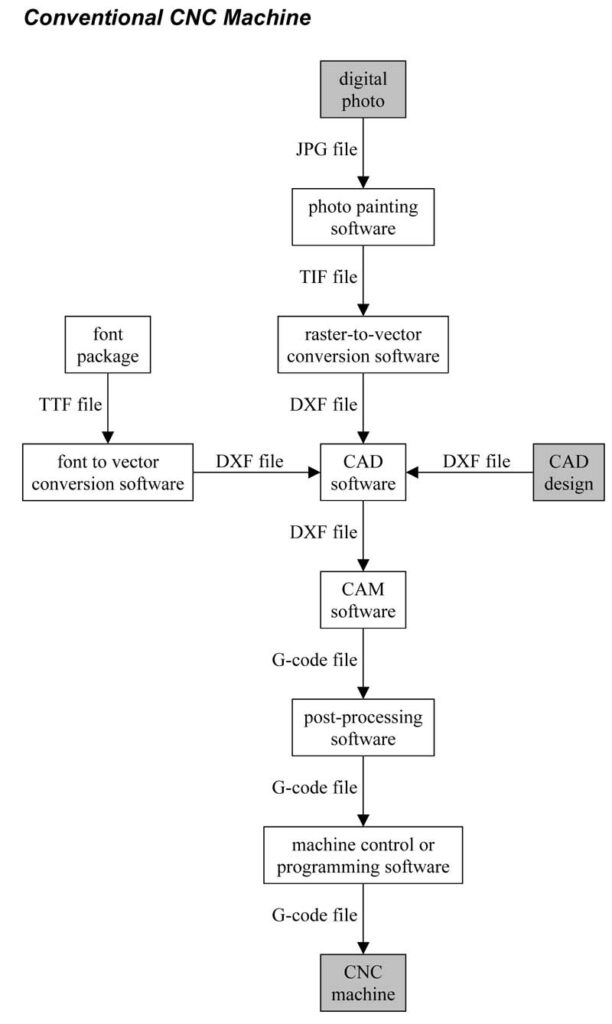
Using Photos
PlasmaCAM
The DesignEdge® software directly reads digital photos and scanned artwork, converting them to vectors using automatic cleanup features designed for plasma cutting. You can even overlay your drawing on a photo to manually trace or alter any special detail from the photo.
Conventional CNC
To cut designs with photos on another CNC machine, you’ll need raster-to-vector conversion software as well as photo painting software that you can use to trace detail in the photo, so the other software can pick up the right edges.
Adding Letters
PlasmaCAM
The DesignEdge software includes over 500 fonts for plasma cutting, and you can use your own fonts. You can draw letters directly from fonts in the software, without having to install them in Windows. Letters can be automatically curved, stenciled, or connected to your design.
Conventional CNC
To cut designs with letters on another CNC machine, you’ll need software that converts fonts to vector files. You’ll also want a package of various fonts you can cut, and these can be difficult to manage in Windows. A lot of manual editing will be required in your CAD software to curve, stencil, or connect letters to your design.
CAD Design
PlasmaCAM
The DesignEdge software can quickly and accurately draw a wide variety of shapes useful for plasma cutting. You can also import designs from other CAD software. The software has powerful editing features not found in other software that increase artistic potential and help you get your design into a solid form that can be cut. detail from the photo.
Conventional CNC
If you use a general CAD program not designed for plasma cutting, you’ll run into many time-consuming or impossible challenges such as limitations in creating artistic designs and trouble combining different pieces together to make a continuous shape that the machine can cut. The learning curve can also be quite steep on these programs.
CAM Process
PlasmaCAM
With one click, the DesignEdge software automatically creates cut paths for your design. It converts and cuts holes in the best order, adds pierce points with lead-ins that give you better edges, and offsets shapes to compensate for the kerf width of the torch. It can use existing edges of the sheet, cut large parts through indexing, and create bend lines in parts. The cut paths become part of the drawing, so you can move and edit them along with your design, change them, etc.
Conventional CNC
With other CNC machines you have to export your finished CAD design to a separate CAM program to build a G-code file. Such programs simply can’t do what DesignEdge does for plasma cutting, so you won’t get as accurate of cut paths and will spend a lot more time reworking designs to get them through the software. The G-code you output often requires manual editing or separate post-processing software to make it compatible with the machine.
Machine Control
PlasmaCAM
The DesignEdge software interactively controls the machine in real time and cuts designs directly from your drawings on screen. You can easily stop, make changes, and re-cut an area. The screen always shows where the torch is, so you can manually move it to where you want to cut a part and move the drawing so the part will cut there.
Conventional CNC
You must upload G-code files to other CNC machines and then run these programs. You may have to transfer them by flash drive to another PC running a different operating system. The entire one-way process from design to programming has to be repeated to make even a small change. If issues arise while cutting, it’s too hard to go back and fix them, so you end up scrapping material and trying again.
Machine Control
PlasmaCAM
The DesignEdge software can import and export many files types including JPG, TIF, BMP, DXF, PLT, PRN, CSV, STL and G-code. It reads everything it can from files without stopping and showing errors. It also writes files formatted to produce the least errors in other software. It can even customize G-code output for another machine so you won’t have to manually edit or post-process the file.
Conventional CNC
Other software programs often show errors and fail to load anything when trying to read file formats like DXF or G-code from another program that formats the file differently. This can make it hard to move designs through all the different programs you need to use, and it may require you to find and use even more programs to reformat files in order to share them between programs.